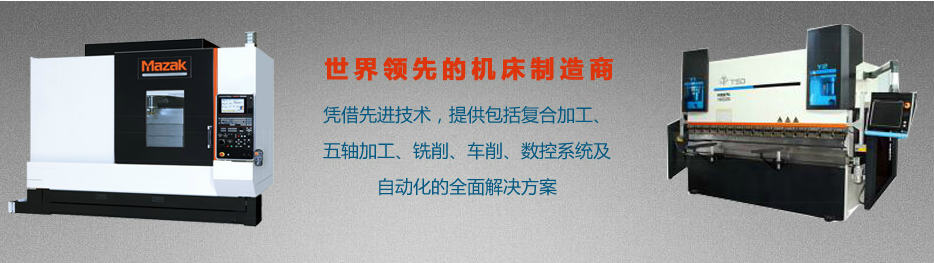
1.節(jié)能改進(jìn)途徑
面向再制造的節(jié)能性改進(jìn)典型的途徑有如下各方面:
(1)電機(jī)由傳統(tǒng)的普通交流異步電機(jī)替代為新型的變頻調(diào)速電機(jī);
(2)傳動(dòng)系統(tǒng)部分將機(jī)械傳動(dòng)結(jié)構(gòu)大為簡(jiǎn)化,使傳動(dòng)鏈大大縮短;
(3)提高機(jī)械結(jié)構(gòu)部件如主軸、導(dǎo)軌等的靜、動(dòng)態(tài)剛度和阻尼精度,使耐磨性提高而熱變形減少,適應(yīng)連續(xù)的自動(dòng)化加工和提高加工生產(chǎn)率;
(4)更多的采用了高效傳動(dòng)部件,如滾珠絲杠副和滾動(dòng)導(dǎo)軌、消隙齒輪傳動(dòng)副等,減小了接觸面之間的摩擦、消除了傳動(dòng)間隙并獲得更高的加工精度;
(5)將機(jī)床導(dǎo)軌改造成為恒流閉式靜壓導(dǎo)軌,這種形式的導(dǎo)軌避免了傳統(tǒng)復(fù)合式導(dǎo)軌靜動(dòng)摩擦系數(shù)差別大,導(dǎo)軌易磨損,定位精度低等缺陷,提高了導(dǎo)軌的剛度,延長(zhǎng)了導(dǎo)軌的使用壽命。
(6)為滿足靜壓油膜可靠建立,導(dǎo)軌必須根據(jù)磨損情況修復(fù)、提精,滿足導(dǎo)軌直線性、平行性和平面度的要求。在導(dǎo)軌結(jié)合面進(jìn)行補(bǔ)充加工,粘貼聚四氟乙烯導(dǎo)軌板,導(dǎo)軌面開設(shè)潤(rùn)滑油槽。
(7)增加了與再制造機(jī)床自動(dòng)化配套的相關(guān)裝置,如刀具自動(dòng)夾緊與換刀裝置、自動(dòng)排屑裝置等輔助裝置,避免了在零件制造過程中,大量的時(shí)間用于更換刀具、裝卸零件、測(cè)量和搬運(yùn)零件等非切削時(shí)間上等等。
為了使機(jī)床的整體能耗情況得到清晰的描述思路和機(jī)床整體節(jié)能方案得到實(shí)施,需要重點(diǎn)對(duì)機(jī)床主要功能模塊的再制造情況及相關(guān)途徑進(jìn)行分析。
2.主傳動(dòng)系統(tǒng)能耗模塊再制造
機(jī)床的主傳動(dòng)系統(tǒng)主要是由主軸電機(jī)、傳動(dòng)系統(tǒng)和主軸組件等構(gòu)成。與再制造之前的機(jī)床相比,傳動(dòng)形式有較大的區(qū)別如圖2.1所示。
機(jī)床經(jīng)過再制造后已經(jīng)大部分或全部取消了主軸箱內(nèi)的齒輪傳動(dòng)系統(tǒng),改由主軸伺服電機(jī)驅(qū)動(dòng),并能實(shí)現(xiàn)無(wú)極自動(dòng)調(diào)速,因而省去了主軸箱內(nèi)較為復(fù)雜的機(jī)械傳動(dòng)鏈,并且主傳動(dòng)與進(jìn)給傳動(dòng)由數(shù)控系統(tǒng)協(xié)調(diào)工作互不影響,故機(jī)床經(jīng)過再制造后的加工精度更高。
該部分的能耗模塊一般包括電機(jī)驅(qū)動(dòng),電機(jī)和機(jī)械傳動(dòng)三個(gè)部分,但主要的損耗發(fā)生在電機(jī)和機(jī)械傳動(dòng)兩部分,如圖2.2所示。
圖2.2主傳動(dòng)能耗模塊的能量損耗輸入功率包含了電機(jī)損耗部分,機(jī)械傳動(dòng)損耗部分和切削區(qū)的功率部分。電機(jī)功率的損耗主要是由于定/轉(zhuǎn)子的鐵損、銅損、摩擦損耗及雜散功率等引起的;而機(jī)械傳動(dòng)部分的損耗則是由于傳動(dòng)件之間的摩擦、阻尼等產(chǎn)生的能量消耗。因此,從能量的角度看,機(jī)床經(jīng)過再制造后傳動(dòng)鏈的縮短不僅提高了傳動(dòng)效率和精度,也在能耗上減少了許多不必要的損耗,達(dá)到了節(jié)能降耗的效果。
3.進(jìn)給系統(tǒng)能耗模塊再制造
再制造前后的進(jìn)給系統(tǒng)也有較大的區(qū)別,再制造之前的進(jìn)給系統(tǒng)是由主傳動(dòng)系統(tǒng)通過掛輪等傳動(dòng)機(jī)構(gòu)驅(qū)動(dòng),沒有獨(dú)立的電機(jī)及控制系統(tǒng)。而再制造之后都有獨(dú)立的電機(jī)及能耗子系統(tǒng)。
進(jìn)給系統(tǒng)的傳動(dòng)系統(tǒng)采用滾珠絲杠的傳動(dòng)形式,把絲杠和螺母旋合螺旋槽之間放置適量的滾珠作為中間滾動(dòng)體,借助于滾珠的作用,將滑動(dòng)接觸變成滾動(dòng)接觸,從而把滑動(dòng)摩擦轉(zhuǎn)化為滾動(dòng)摩擦,減小了摩擦損耗。
再制造之前,進(jìn)給系統(tǒng)的傳動(dòng)鏈較長(zhǎng)且復(fù)雜,經(jīng)過再制造后若采用伺服直驅(qū)的進(jìn)給方式,可取消從電動(dòng)機(jī)到工作臺(tái)間的中間環(huán)節(jié),這樣進(jìn)給傳動(dòng)鏈縮短為零,提高了加工可靠性的同時(shí),也減少了相應(yīng)環(huán)節(jié)的能量損耗。
4.冷卻潤(rùn)滑系統(tǒng)能耗模塊再制造
機(jī)床的冷卻潤(rùn)滑系統(tǒng)通過再制造后,將原有的集中潤(rùn)滑形式改變?yōu)楦麟姍C(jī)分別控制的模式。根據(jù)各潤(rùn)滑冷卻作用處的油液壓力和流量等的大小不同及功能差異,采用分開獨(dú)立供油的方式。這樣的好處是可以根據(jù)加工過程的實(shí)際情況按照需求供應(yīng)冷卻液和潤(rùn)滑液。如圖4.1所示為某機(jī)床再制造后的冷卻潤(rùn)滑系統(tǒng)圖:
由圖可知,供應(yīng)各處的潤(rùn)滑油和冷卻液需要的排量和產(chǎn)生的壓力都由相應(yīng)的儀表進(jìn)行顯示,各液路按所需的油量分配到潤(rùn)滑和冷卻點(diǎn),同時(shí)由控制器完成各自點(diǎn)的潤(rùn)滑冷卻時(shí)間、潤(rùn)滑冷卻次數(shù)、故障報(bào)警以及停機(jī)的控制,實(shí)現(xiàn)自動(dòng)控制和按需分配的目的。對(duì)于機(jī)床液壓部分油液溫度的控制將在后續(xù)關(guān)鍵技術(shù)部分做更詳細(xì)的介紹。
5.液壓系統(tǒng)能耗模塊再制造
將機(jī)床的液壓系統(tǒng)由原來(lái)的集中供油的方式進(jìn)行分散化處理。機(jī)床采用兩套液壓系統(tǒng),一套負(fù)責(zé)給機(jī)床床身、滑座、主軸箱提供給靜壓油和潤(rùn)滑油,這是主要部分。另一套功率相對(duì)較小,負(fù)責(zé)提供主軸刀具、主軸變速、主軸箱液壓補(bǔ)償?shù)扔糜?。兩套系統(tǒng)共用一個(gè)油箱,且對(duì)應(yīng)各處的油液供應(yīng)都有相應(yīng)的變頻電機(jī)進(jìn)行流量的調(diào)節(jié)。如圖5.1所示為某大型機(jī)床進(jìn)行再制造后的液壓油箱。
6.其他能耗模塊再制造
其他能耗模塊的再制造內(nèi)容主要是改進(jìn)了用于輔助工序的自動(dòng)化裝置,如自動(dòng)換刀裝置和自動(dòng)排屑裝置等。
與再制造之前的機(jī)床相比,自動(dòng)換刀裝置一方面可避免多次定位帶來(lái)的誤差,另一方面減少了因多次安裝造成的輔助時(shí)間,從而提高了勞動(dòng)生產(chǎn)率和設(shè)備利用率,也減少了這段時(shí)間機(jī)床運(yùn)行而產(chǎn)生的能耗。自動(dòng)排屑裝置使原有機(jī)床切屑堆積的問題得到妥善解決,及時(shí)地將機(jī)床產(chǎn)生的切削排除出去,從而有效保證機(jī)床的高效、可靠的穩(wěn)定運(yùn)行。根據(jù)機(jī)床結(jié)構(gòu)的特點(diǎn),自動(dòng)排屑裝置有平板鏈?zhǔn)?、刮板式和螺旋式三種形式。