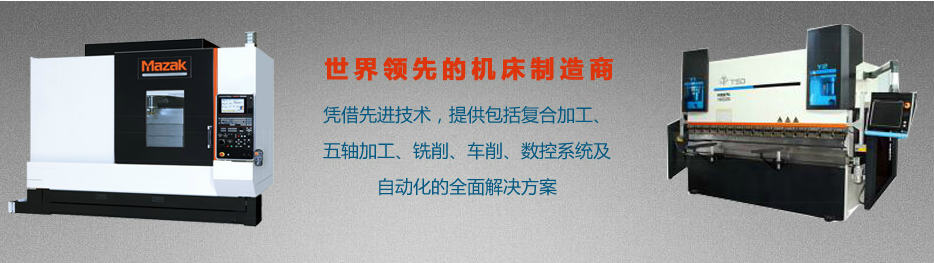
1.定位膠灌膠工藝
在機(jī)床生產(chǎn)過(guò)程中,設(shè)計(jì)及裝配人員經(jīng)常會(huì)遇到機(jī)床零部件的固定連接和定位問(wèn)題。為了達(dá)到零部件精度要求,同時(shí)還要保持精度的長(zhǎng)期穩(wěn)定性,這需要工件既要滿足橫向、縱向及垂直的精度要求,又要使接觸面積均勻,達(dá)到75%以上,需要進(jìn)行結(jié)構(gòu)定位。
傳統(tǒng)的結(jié)構(gòu)定位主要依靠機(jī)械方法定位,一般需對(duì)零部件先進(jìn)行精加工,然后再進(jìn)行刮研處理,或經(jīng)多次拆裝來(lái)達(dá)到要求,在精度完全調(diào)整好后還要配裝銷釘,或者在零件平面間設(shè)計(jì)楔鐵進(jìn)行調(diào)整,再用螺栓鎖死。這種操作方式效率低下,而且難以檢驗(yàn),容易導(dǎo)致裝配質(zhì)量不可靠。
最近幾年在國(guó)內(nèi)外機(jī)床行業(yè)中廣泛的應(yīng)用了定位膠技術(shù),滿足了機(jī)床生產(chǎn)廠家高精、高速、高穩(wěn)定性的需求。
定位膠技術(shù)采用高強(qiáng)度定位膠對(duì)調(diào)整好精度的零部件結(jié)合面進(jìn)行灌膠固定,操作簡(jiǎn)單、調(diào)整方便、降低裝配難度,增大結(jié)構(gòu)結(jié)合面,越來(lái)越多的被應(yīng)用于例如平面結(jié)構(gòu)的無(wú)銷釘定位、大尺寸齒圈導(dǎo)軌的定位、軸套與箱體的結(jié)構(gòu)定位、直線導(dǎo)軌的定位中。
2.灌膠技術(shù)的工藝方案
在生產(chǎn)過(guò)程中,各部件在完成部裝后在用戶方的安裝調(diào)整順序主要分為以下幾步:
(1)底座的安裝及調(diào)平;
(2)床身的安裝及調(diào)平;
(3)立柱在床身及滑座上的調(diào)整及安裝;
(4)橫梁的安裝及調(diào)平等;
其中立柱在床身及滑座上的調(diào)整難度較大,且對(duì)后續(xù)的橫梁精度及機(jī)床工作精度影響較大。
在傳統(tǒng)安裝過(guò)程中,是在機(jī)床各部件進(jìn)行裝配后,然后進(jìn)行機(jī)床總裝調(diào)試,并檢測(cè)立柱和橫梁的幾何數(shù)據(jù),此時(shí)立柱的前傾、后仰數(shù)據(jù)僅為調(diào)試數(shù)據(jù),為下一工序的滑座(立柱下)返修提供數(shù)據(jù)支持,根據(jù)檢測(cè)結(jié)果對(duì)比要求的設(shè)計(jì)值對(duì)滑座進(jìn)行返修。此返修工序?qū)ιa(chǎn)裝配有幾項(xiàng)要求:
1)有此返修加工能力的機(jī)床;
2)所提供的返修加工數(shù)據(jù)準(zhǔn)確無(wú)誤;
3)不能影響下一步裝配周期。
這種返加工工序拖長(zhǎng)機(jī)床的生產(chǎn)周期,不能很好的保證機(jī)床的安裝質(zhì)量。
采用定位膠技術(shù)可以很好的解決以上的問(wèn)題,其工藝方法如下:
(1)膠層厚度
經(jīng)過(guò)研究和模擬試驗(yàn)測(cè)試,并查閱相關(guān)資料,此類定位膠的成分和種類,其膠層厚度對(duì)膠層的最終物理性能有較大影響,間隙在1.5~2mm的膠層厚度其物理性能較為理想,接觸面積大,抗壓強(qiáng)度≥120MPa,固化收縮率0.06~0.08%,能夠滿足使用要求,因此我們確定在項(xiàng)目機(jī)床的立柱和滑座中間灌注2mm的膠層厚度。
圖2.2膠層示意圖
(2)調(diào)整方案
本文所研究的機(jī)床立柱部件、橫梁部件、刀架及升降設(shè)備等件的重量,使滑座與立柱結(jié)合面受力達(dá)到500~800余噸,如何在兩部件結(jié)合面中間調(diào)整出2mm的間隙方案如下:
在注膠腔位置粘結(jié)3mm厚膠條,內(nèi)圈放置調(diào)整墊鐵、外圈放置楔鐵
圖2.3 注膠腔方案圖
方案優(yōu)點(diǎn):第一可以避免在外圈復(fù)雜區(qū)域內(nèi)放置調(diào)整墊鐵的問(wèn)題,第二結(jié)合面以下重量由內(nèi)圈調(diào)整墊鐵、外圈楔鐵和定位膠層共同負(fù)載(注膠后使用過(guò)程中主要由膠層受力),第三調(diào)整墊可以調(diào)整立柱前傾后仰數(shù)據(jù),應(yīng)用價(jià)值較大。因此,我們選用該方案進(jìn)行此次灌膠操作,共計(jì)在滑座體內(nèi)圈表面加工墊鐵槽12個(gè),外圈表面加工楔鐵槽8個(gè),設(shè)計(jì)膠腔27個(gè)。
(3)膠層受力
本文設(shè)計(jì)的27個(gè)膠腔總面積為:3425825mm2;
立柱左側(cè)膠層面積:784237mm2;
立柱前側(cè)膠層面積:1013811mm2;
立柱左前點(diǎn)膠層面積:671737mm2;
設(shè)計(jì)承載立柱部件重332噸,橫梁部件重92.8噸,以及刀架、升降設(shè)備等件共計(jì)550噸;
平均載荷:
左側(cè)最大載荷:
前側(cè)最大載荷:
極限載荷:
機(jī)床集中于膠層的極限載荷為8.642MPa,遠(yuǎn)遠(yuǎn)小于定位膠的抗壓強(qiáng)度,而且立柱與滑座四周方向均布90個(gè)M36的緊固螺釘,因此膠層不會(huì)承受拉力,安全余量很大,可以滿足機(jī)床的承重需求。
(4)灌膠方案
圖2.4灌膠方案示意圖
膠腔的注膠方案采取每個(gè)膠腔加兩個(gè)膠孔,一進(jìn)一出的方法進(jìn)行注膠如圖所示,兩膠孔均靠近膠腔邊線,注膠孔較出膠孔深靠近膠內(nèi)部,出膠孔靠近膠腔邊緣,注膠時(shí)有利于填滿整個(gè)膠腔。共計(jì)在滑座大件表面加工注膠孔27個(gè),出膠孔27個(gè)。
3.灌膠技術(shù)的試驗(yàn)使用
為保證此次灌膠工藝技術(shù)在項(xiàng)目機(jī)床上得到成功運(yùn)用,并獲得第一手的使用經(jīng)驗(yàn)數(shù)據(jù),我們選取了正在安裝的機(jī)床進(jìn)行了試驗(yàn)應(yīng)用。
3.1灌膠實(shí)施過(guò)程
3.1.1零部件清理
清理立柱與滑座結(jié)合面;在立柱下底面上噴涂“脫模劑”(距四周各邊約400范圍內(nèi)),以便于拆卸;在立柱與滑座四周和注膠孔與出膠孔周圍噴涂脫模劑,便于清除表面固化后的定位膠;在滑座上表面上劃線,按圖紙尺寸用“瞬干膠”粘結(jié)“橡膠密封條”,要求密封腔體閉合良好;在定位膠腔體內(nèi)的螺栓孔周圍粘結(jié)“O型密封墊”。
3.1.2立柱調(diào)整
在滑座內(nèi)圈開(kāi)槽處,均勻放置12個(gè)調(diào)整楔鐵,預(yù)調(diào)墊鐵高度一致,并高出滑座上表面2mm;吊裝立柱于內(nèi)圈楔鐵上;天車勾吊立柱,使立柱平穩(wěn)支撐在墊鐵和楔鐵上,調(diào)整內(nèi)圈楔鐵使立柱后仰、右傾值達(dá)到設(shè)計(jì)要求;預(yù)緊立柱與滑座四周緊固螺釘;按此時(shí)立柱的位置調(diào)整外圈的8個(gè)立柱定位楔鐵,并對(duì)楔鐵與立柱的結(jié)合面進(jìn)行配刮,要求接觸點(diǎn)數(shù)達(dá)到6~8點(diǎn)/25×25mm2,達(dá)到要求后把緊楔鐵端頭螺釘;
3.1.3實(shí)施灌膠
調(diào)膠:取出定位膠,將A組膠先攪拌均勻后,再將B組膠倒入,攪拌均勻;將攪拌均勻的定位膠導(dǎo)入膠筒,推入尾塞,膠筒出膠口向上,使膠流向底部后,將膠嘴切開(kāi),安裝注膠尖嘴并裝入注膠槍,排除膠筒上部空氣;通過(guò)注膠孔將定位膠緩慢注入,當(dāng)出膠孔出膠后停止注膠,并繼續(xù)保持半分鐘左右,以保證填滿整個(gè)腔體;注膠時(shí)要根據(jù)膠的性能和操作手冊(cè)進(jìn)行。達(dá)到操作手冊(cè)所要求的固話時(shí)間后,取下膠堵,檢查膠腔內(nèi)定位膠固化狀態(tài),如無(wú)異常,均勻緊固把緊固螺釘,復(fù)檢機(jī)床各項(xiàng)幾何精度,完成灌膠操作和機(jī)床安裝。
通過(guò)對(duì)機(jī)床進(jìn)行了灌膠實(shí)驗(yàn),驗(yàn)證了該項(xiàng)技術(shù)的可靠性,提出了灌膠工藝方案,縮短了生產(chǎn)周期,提高了立柱定位精度和定位質(zhì)量。