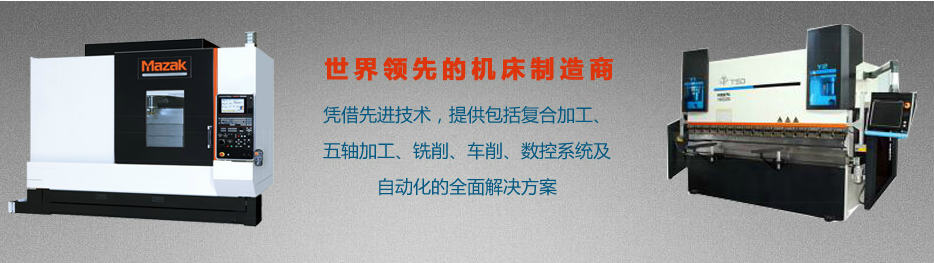
一、宏觀產(chǎn)品質(zhì)量控制方法
建立質(zhì)量保證體系,企業(yè)必須全面開展質(zhì)量管理工作,加強基礎(chǔ)工作,搞好質(zhì)量控制。在生產(chǎn)流程的各個階段,將個人的責(zé)任按照規(guī)定有機的聯(lián)系在一起,形成保證質(zhì)量的體系,實現(xiàn)各項工作的標(biāo)準(zhǔn)化、程序化和高效化。
工序控制是最主要的影響鑄件質(zhì)量控制的因素,工序控制首先要按工序流程確定好控制點,將一些生產(chǎn)過程中數(shù)據(jù)作為質(zhì)量控制過程關(guān)鍵參數(shù)。原則上選取容易發(fā)生質(zhì)量缺陷和對鑄件質(zhì)量影響較大的因素確定為控制點,根據(jù)控制點指定控制內(nèi)容、依據(jù)標(biāo)準(zhǔn)、控制方法和手段等。在各個控制點建立報告單、記錄表等,進行自檢、互檢和專檢,并做好預(yù)防為主,提前做好確保機床鑄件質(zhì)量的準(zhǔn)備工作。
同時,要對實施鑄造工藝的工人進行工藝交底,讓工人從思想上認識工藝、掌握工藝,并補充、完善和改進工藝。在此過程中,車間技術(shù)人員也將工藝實施細則進行交底,使工人明確控制的重點,從而自覺自愿地執(zhí)行工藝,調(diào)動了工人的主動性和創(chuàng)造性。管理者要在造型中檢驗把關(guān),做好質(zhì)量管理控制關(guān)。
由公司用戶服務(wù)處牽頭,在外建立客戶質(zhì)量信息網(wǎng),及時把質(zhì)量信息傳遞給有關(guān)負責(zé)部門。在生產(chǎn)內(nèi)部,明確規(guī)定下道工序就是上道工序的用戶,不能把責(zé)任下推。不同工藝部門要建立好互訪和反饋的協(xié)調(diào)關(guān)系,不斷分析問題,解決問題,提高質(zhì)量。
二、造型和制芯部分的關(guān)鍵技術(shù)
造型和制芯過程中的每個細節(jié)都會影響機床成品鑄件的穩(wěn)定性和一致性,在這其中,最主要的關(guān)鍵問題是造型的選擇、型砂的質(zhì)量、制殼工序的控制。
在機床行業(yè)鑄件中,常用的造型包括:整體模兩箱造型、分開模兩箱造型、挖割造型、假箱造型、挖板造型、地坑造型和三箱造型。造型方法多種多樣,各有利弊時一個零件可有多種造型方法供選擇,在選擇時,應(yīng)首先考慮滿足零件的質(zhì)量要求,然后考慮工藝簡單、生產(chǎn)效率高、成本低而生產(chǎn)條件允許的造型方法。
對于鑄件的缺陷來說,造成氣孔缺陷的主要因素包括型砂的透氣性、濕抗壓強度和水分、坭芯和鑄型的排氣是否通暢等。砂眼缺陷產(chǎn)生的主要原因包括:鑄型或型芯及涂料強度不夠,混砂不均勻;型砂太濕或含氣體物質(zhì)過多。因此,在選擇材料的化學(xué)成分的同時,一定要考慮到這些環(huán)節(jié)上的控制。
對于鑄件表面和近表面的缺陷來說,制殼工藝的操作不當(dāng)、控制不嚴(yán)是產(chǎn)生這些缺陷的主要原因。因此,必須加強對制殼工序面層和干燥過程的控制,盡量減少面層裂紋的產(chǎn)生。面層干燥濕度穩(wěn)定在80%~90%范圍內(nèi),保持生產(chǎn)環(huán)境的溫度、濕度均勻??刂坪猛苛蠞{的粘度、pH值等指標(biāo)進行分析,確保涂料漿成分和性能的穩(wěn)定。減少蠟在型殼內(nèi)殘留的數(shù)量,多次反復(fù)脫蠟。
三、熔煉和澆注部分的關(guān)鍵技術(shù)
目前機床鑄件大部分為灰鑄鐵,高碳當(dāng)量、高強度是灰鑄鐵的發(fā)展方向,提高灰鑄鐵的冶金質(zhì)量,需要在熔煉和澆注環(huán)節(jié)抓住關(guān)鍵節(jié)點,提高質(zhì)量。在熔煉環(huán)節(jié),要注意把握碳當(dāng)量的控制。高碳當(dāng)量是灰鑄鐵在高強度下獲得低鑄造應(yīng)力、良好的加工性和柱造性的必經(jīng)途徑,目前,國內(nèi)的機床鑄件碳當(dāng)量比國外機床鑄件的碳當(dāng)量對比要低,可適量提高。同時,較高的硅碳比能有效防止在薄壁出產(chǎn)生白口,有利于提高鑄件組織的均勻性、強度、硬度,并減少殘留應(yīng)力,然而,當(dāng)碳當(dāng)量較高時,鑄鐵組織中出現(xiàn)鐵素體的機會明顯增大,這對提高鑄件的綜合性能極為不利,因此,硅碳比最好控制在0.6左右。鐵液中加入合金元素能夠增加并細化珠光體,強化鐵素體,細化石墨,細化共晶團,改善界面敏感性。在高碳當(dāng)量下需要加入某些穩(wěn)定珠光體的合金元素以增強其強度和硬度,減少界面敏感性。低合金化也是機床鑄件熔煉不可缺少的措施。在熔煉過程中,還有適當(dāng)調(diào)整配料的配比,生鐵加入量一般低于10%,廢鋼配比適時提高,并控制鐵液溫度為1500~1550℃。
在澆注部分,鐵水中的化學(xué)成分對質(zhì)量有很大影響。如碳是形成滲碳體的元素,含碳量增加則滲碳體數(shù)量增加,因而硬度增加。適當(dāng)提高原鐵液碳當(dāng)量,一方面增加了凝固時的石墨化膨脹,另一方面降低了爐前孕育量,避免造成過孕育而引起的共晶團數(shù)急劇增加,因此能夠降低縮松滲漏傾向;但碳當(dāng)量過高容易造成孕育量不足,石墨粗大,降低鑄件力學(xué)性能。在澆注過程中,澆注系統(tǒng)中的泥砂、溶蝕的流鋼磚或脫氧產(chǎn)物,從模內(nèi)鋼液中浮出來,被正在凝固的錠殼捕獲,而形成夾砂。由于精煉變質(zhì)處理后除渣不干凈,或是精煉變質(zhì)后靜置時間不夠,澆注系統(tǒng)不合理,精煉后合金液攪動或被污染等造成的,當(dāng)保護渣熔化不良時,也會被上升的鋼液卷入表層而形成夾渣。為防止夾砂的形成,必須時常清掃澆注系統(tǒng)并改善保護渣配方。此外,如果澆道設(shè)置不準(zhǔn)確,澆注時發(fā)生沸騰,而使型砂進入金屬液,造成鑄型緊實不均勻,合箱時鑄型或型芯被破損等。因此,澆注環(huán)節(jié)主要要注意模具的澆道要設(shè)置準(zhǔn)確,排氣道和溢流要做得好,設(shè)置準(zhǔn)確的金屬液體的化學(xué)成分,包括碳、硅、磷、鈦、稀土殘余和鎂殘余等,合金澆注溫度要適當(dāng)提升,控制好澆注溫度,并控制好沙箱濕度。
四、后處理部分的關(guān)鍵技術(shù)
后處理工藝從冷卻、開箱、落沙、澆口分離、拋丸、毛整、除銹,然后裝箱。后處理工藝主要對鑄件的定型和完成的一些細節(jié)進行有效的處理,從而控制鑄件的尺寸、應(yīng)力、表面粗糙度和形狀等。如果后處理工藝進行的不夠完全和仔細,則很容易造成整個工藝流程的前功盡棄,降低鑄件產(chǎn)品的合格率。這是作為質(zhì)量管理最不愿意看到的。然而,后處理工藝往往是整個質(zhì)量控制環(huán)節(jié)最容易忽視的環(huán)節(jié),需要在落砂、毛整和除銹設(shè)置關(guān)鍵結(jié)點,進行質(zhì)量把控。此外,在產(chǎn)品檢測方面,務(wù)必要完善金相組織的檢驗,并設(shè)立對彈性模量、鑄造應(yīng)力、鑄件變形的檢驗。
機床鑄件的質(zhì)量與整個機械制造業(yè)關(guān)系極為密切,在一定程度上代表了一個國家的鑄造水平。提高機床鑄件質(zhì)量是一整套的技術(shù)控制過程,必須把技術(shù)環(huán)節(jié)和質(zhì)量管理有機地結(jié)合在一起,合理有效地加以控制。